Lathe accidents pose a significant threat to safety in industrial environments and workshops. These versatile machines, essential for manufacturing, can lead to severe injuries if not handled with care and proper safety protocols. Understanding the causes, prevention methods, and safety measures is crucial for reducing these incidents and ensuring a safer workplace.
Each year, countless accidents involving lathes occur, resulting in injuries ranging from minor cuts to life-altering disabilities. Recognizing the hazards associated with lathe machines is critical. Workers must be trained to identify potential dangers and take appropriate precautions to ensure their safety and well-being.
This article delves into the complexities of lathe accidents, offering insights into their causes, preventive measures, and the importance of adhering to safety protocols. By the end of this guide, you will have a thorough understanding of how to mitigate risks and foster a safer working environment.
Read also:Peter Stormare In Prison Break
Table of Contents
- Understanding Lathe Accidents
- Identifying Common Causes of Lathe Accidents
- Lathe Accident Statistics
- Safety Measures to Prevent Lathe Accidents
- The Importance of Comprehensive Training
- Developing Effective Emergency Procedures
- Navigating the Legal Implications of Lathe Accidents
- Case Studies: Real-Life Examples of Lathe Accidents
- Technological Innovations in Lathe Safety
- Conclusion
Understanding Lathe Accidents
Lathe machines are indispensable in the manufacturing industry, used for shaping metal, wood, and other materials. However, their complexity and power make them potentially hazardous when not operated correctly. Lathe machines are responsible for a significant number of workplace accidents, underscoring the importance of understanding the nature of these incidents.
Many lathe accidents occur due to operator error, insufficient training, or improper machine maintenance. By identifying and addressing these factors, we can develop effective strategies to minimize the likelihood of accidents and enhance workplace safety.
Identifying Common Causes of Lathe Accidents
Lathe accidents can stem from a variety of factors, both human and mechanical. Below are some of the most common causes:
- Inadequate Training: Operators lacking proper training are more prone to making mistakes that can lead to accidents.
- Improper Use of Equipment: Using the wrong tools or failing to follow established procedures increases the risk of injury.
- Poor Machine Maintenance: A lathe machine that is not regularly maintained is more likely to malfunction, leading to accidents.
- Distracted Operators: Operators who are distracted or not fully focused on their work are more likely to experience accidents.
Lathe Accident Statistics
Data from the Occupational Safety and Health Administration (OSHA) highlights alarming statistics regarding lathe accidents. According to their reports:
- Approximately 30% of all machine-related injuries in manufacturing involve lathes.
- Over 10,000 lathe-related injuries are reported annually in the United States alone.
- Severe injuries, such as amputations and fractures, account for nearly 20% of all lathe accidents.
These statistics emphasize the urgent need for improved safety measures and enhanced training programs to address the risks associated with lathe machines.
Safety Measures to Prevent Lathe Accidents
Implementing comprehensive safety measures is essential to reducing the incidence of lathe accidents. Below are some effective strategies:
Read also:Who Is Morgan Freeman S Son
The Role of Personal Protective Equipment
Wearing the appropriate personal protective equipment (PPE) is crucial for operator safety. Key PPE items include:
- Safety goggles to protect against flying debris and ensure clear vision.
- Gloves to prevent cuts, abrasions, and other hand injuries.
- Hearing protection to reduce noise exposure and prevent hearing damage.
The Importance of Regular Machine Maintenance
Regular maintenance of lathe machines is vital to ensure they function correctly and safely. Key maintenance tasks include:
- Inspecting and replacing worn-out parts to prevent malfunctions.
- Ensuring proper lubrication and alignment to maintain machine efficiency.
- Verifying that all safety guards are in place and functioning properly.
The Importance of Comprehensive Training
Proper training is one of the most effective ways to prevent lathe accidents. Training programs should cover:
- The correct operation of lathe machines, including setup and shutdown procedures.
- The importance of adhering to safety protocols and guidelines.
- How to handle emergencies and respond effectively to accidents.
Regular refresher courses and hands-on practice sessions can reinforce learning and improve operator confidence, ultimately reducing the risk of accidents.
Developing Effective Emergency Procedures
Having clear and well-practiced emergency procedures in place is crucial for minimizing the impact of lathe accidents. Key steps include:
- Immediate shutdown of the machine in the event of an accident to prevent further injury.
- Providing first aid to injured personnel until professional medical help arrives.
- Documenting the incident thoroughly for future analysis and prevention.
Employees should be familiar with these procedures and regularly participate in drills and simulations to ensure readiness in case of an emergency.
Navigating the Legal Implications of Lathe Accidents
Lathe accidents can have significant legal implications for both employers and employees. Employers may face lawsuits, fines, and penalties if they fail to comply with safety regulations. Employees, on the other hand, may be entitled to compensation for injuries sustained due to workplace negligence.
Understanding the legal landscape surrounding lathe accidents is essential for all parties involved. Consulting with legal experts and ensuring compliance with OSHA regulations can help mitigate risks and liabilities, protecting both employers and employees.
Case Studies: Real-Life Examples of Lathe Accidents
Examining real-life case studies provides valuable insights into the causes and consequences of lathe accidents. For instance:
- A worker in a manufacturing plant suffered a severe hand injury when a lathe machine malfunctioned due to a lack of regular maintenance.
- In another incident, an inexperienced operator failed to wear safety goggles, resulting in eye damage from flying metal shavings.
These examples highlight the critical importance of proper training and regular maintenance in preventing accidents and ensuring workplace safety.
Technological Innovations in Lathe Safety
Advancements in technology have significantly improved lathe safety. Modern lathes are equipped with features such as:
- Automatic shut-off systems that activate in the event of malfunctions, preventing further injury.
- Sensors that detect operator presence and adjust machine settings accordingly, enhancing safety.
- Enhanced safety guards that minimize the risk of contact with moving parts, reducing the likelihood of accidents.
Embracing these technological innovations can greatly enhance workplace safety and reduce the incidence of lathe accidents.
Conclusion
Lathe accidents are a serious concern in industrial environments, but they are preventable with the right safety measures and protocols in place. By understanding the causes, implementing preventive strategies, and utilizing technological advancements, we can create safer working conditions for all.
We encourage readers to share their thoughts and experiences in the comments section below. Additionally, feel free to explore other articles on our site for more insights into workplace safety and industrial practices. Together, we can work toward a future where lathe accidents become a thing of the past.
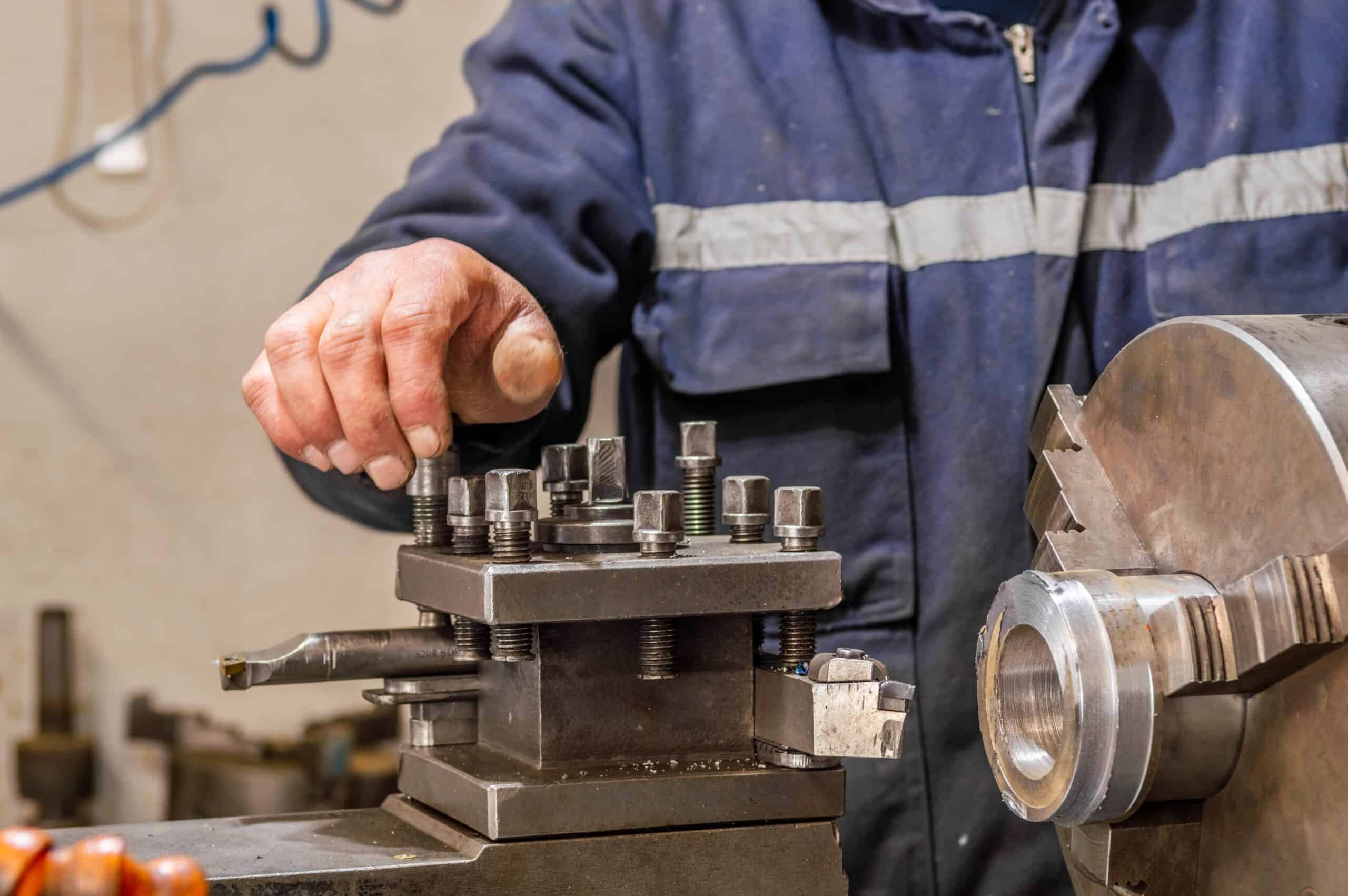
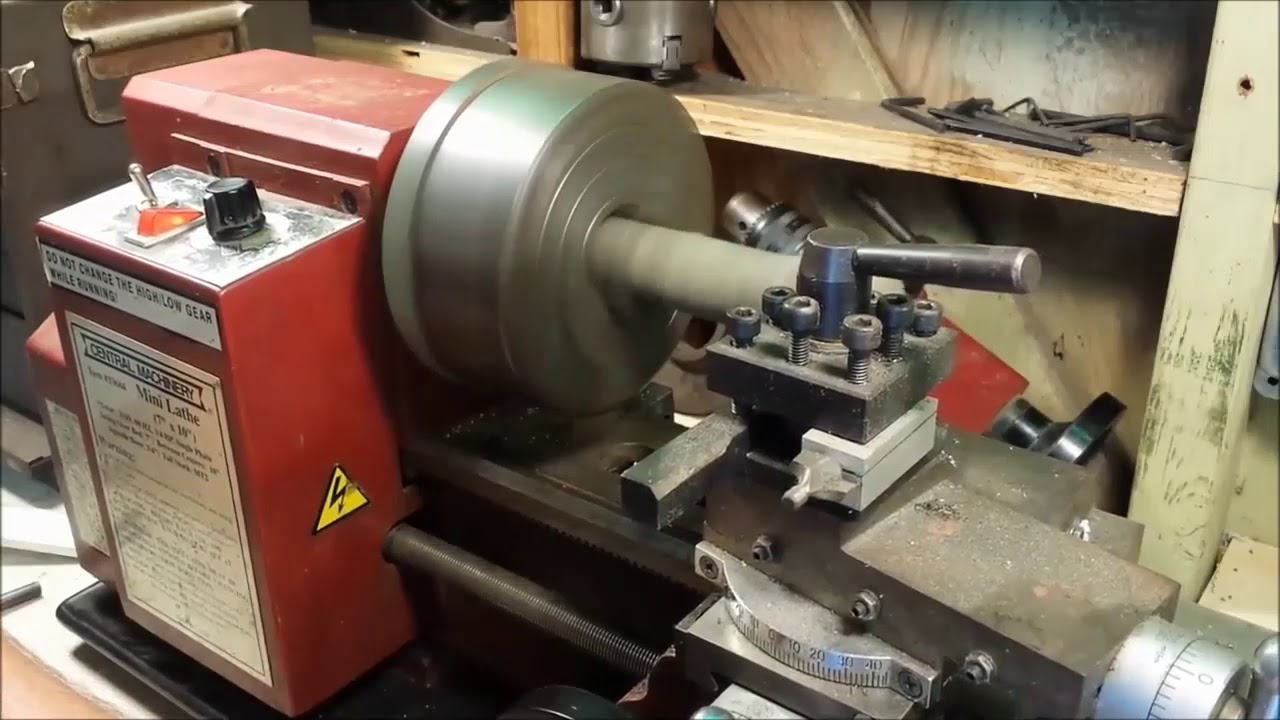
