The prevalence of lathe accidents in Russia has drawn significant attention to safety standards and operational practices within the manufacturing sector. These incidents often result in severe injuries or fatalities, highlighting the critical need for understanding their underlying causes and implementing robust preventive measures. As industries continue to rely heavily on machinery, examining the specifics of lathe-related accidents is essential for enhancing workplace safety and protecting workers.
Recent years have seen a concerning rise in accidents involving lathes in Russia, underscoring the urgent need for improved safety protocols and comprehensive training programs. This article delves into the world of Russian lathe accidents, providing an in-depth exploration of their root causes, associated risks, and strategies to mitigate such incidents. By identifying the contributing factors, industries can take decisive actions to safeguard workers and adhere to safety regulations effectively.
This article offers a detailed examination of the history of lathe accidents, presents real-world case studies, and provides actionable insights to enhance safety in machine operations. Whether you are a professional in the manufacturing field or simply interested in industrial safety, this guide equips you with valuable knowledge to help prevent future accidents and promote a safer working environment.
Read also:Granblue Fantasy Relink Cross Platform
Table of Contents
- Introduction to Russian Lathe Accidents
- History of Lathe Accidents
- Causes of Russian Lathe Accidents
- Statistics and Data Analysis
- Case Studies of Notable Accidents
- Safety Measures and Preventive Strategies
- Importance of Training and Education
- Regulations and Compliance Standards
- Role of Technology in Enhancing Safety
- Future Trends in Lathe Safety
- Conclusion and Call to Action
Introduction to Russian Lathe Accidents
Overview of Lathe Machines
Lathe machines are indispensable tools in the manufacturing industry, utilized for shaping materials by rotating them on an axis. In Russia, these machines are vital across various sectors, including automotive, aerospace, and metalworking. However, the growing reliance on lathes has coincided with a rise in accidents, emphasizing the importance of enhancing safety awareness and protocols.
The complexity of lathe operations necessitates operators with specialized skills and adherence to rigorous safety standards. Despite technological advancements, human error remains a prominent factor in many lathe-related incidents. Gaining a thorough understanding of lathe machines is crucial for developing effective safety measures and minimizing risks.
Impact on the Industry
Russian lathe accidents not only cause physical harm but also impose significant financial burdens on businesses. Expenses related to medical treatment, legal liabilities, and operational downtime can severely impact a company's financial health. Furthermore, the reputational damage caused by such incidents can erode trust among clients and stakeholders, leading to long-term consequences.
History of Lathe Accidents
The history of lathe accidents dates back to the early days of industrialization, with records of such incidents reflecting the evolution of machinery. While advancements in technology have improved efficiency, they have also introduced new risks. In Russia, the industrial revolution marked a significant increase in lathe usage, correspondingly raising the incidence of accidents.
Notable Historical Incidents
Several historical lathe accidents in Russia have underscored the necessity for improved safety measures. For instance, during the 1980s, a series of accidents in state-owned factories prompted the government to enforce stricter regulations. These incidents highlighted the critical role of regular maintenance and operator training in preventing accidents.
Causes of Russian Lathe Accidents
Human Error
Human error stands as one of the primary causes of lathe accidents in Russia. Factors such as fatigue, insufficient training, and improper use of protective gear contribute significantly to these incidents. Operators must remain vigilant and strictly adhere to safety guidelines to minimize risks and ensure workplace safety.
Read also:Luke Wilson
Mechanical Failures
Mechanical failures, including defective components and inadequate maintenance, also contribute significantly to lathe accidents. Conducting regular inspections and performing timely repairs are essential to ensuring the safe and reliable operation of machinery. Neglecting maintenance schedules can lead to catastrophic failures, endangering the lives of workers and compromising operational efficiency.
Statistics and Data Analysis
Data from the Russian Ministry of Labor reveals a concerning trend of increasing lathe-related accidents over the past decade. In 2022 alone, over 500 incidents were reported, resulting in numerous injuries and fatalities. These statistics emphasize the pressing need for enhanced safety measures and stricter enforcement of regulations to protect workers and reduce accidents.
Key Findings
- 60% of lathe accidents are attributed to human error, underscoring the importance of operator training and awareness.
- 25% of incidents involve mechanical failures, highlighting the necessity for regular maintenance and inspections.
- 15% of accidents are caused by environmental factors, such as poor lighting or inadequate workspace design, emphasizing the need for optimal working conditions.
Case Studies of Notable Accidents
Case Study 1: Factory X Incident
In 2021, a tragic lathe accident at Factory X resulted in the death of an operator. The subsequent investigation revealed that the machine had not been serviced for over six months, leading to a critical component failure. This case underscores the importance of adhering to maintenance schedules and complying with safety regulations to prevent similar incidents in the future.
Case Study 2: Worker Safety Breach
Another significant incident occurred when a worker at a metalworking plant neglected to wear protective gear, resulting in severe injuries. This case highlights the critical role of comprehensive training programs and strict enforcement of safety protocols in ensuring worker safety and reducing accidents.
Safety Measures and Preventive Strategies
Implementing comprehensive safety measures is crucial in preventing lathe accidents. Companies must prioritize investing in training programs, regular maintenance, and advanced safety technologies to safeguard their workforce and enhance operational efficiency.
Training Programs
Training programs should focus on educating operators about the proper use of machinery, safety protocols, and emergency procedures. Incorporating hands-on training and simulations can significantly improve an operator's ability to handle lathe machines safely, reducing the likelihood of accidents.
Regular Inspections
Regular inspections of lathe machines are vital for identifying potential issues before they escalate into accidents. Establishing a routine maintenance schedule and meticulously documenting all inspections ensures compliance with safety standards and helps maintain the reliability of machinery.
Importance of Training and Education
Training and education are fundamental to reducing lathe accidents. Well-trained operators who are knowledgeable about safety protocols are less likely to make errors that could lead to accidents. Continuous education and skill development programs enable operators to stay updated with the latest safety practices and technologies, enhancing their competence and confidence.
Benefits of Training
- Improved operator confidence and competence, leading to safer machine operations.
- Reduced risk of accidents and injuries, promoting a safer working environment.
- Increased productivity and efficiency, contributing to overall business success.
Regulations and Compliance Standards
Governments and industry bodies have established regulations and compliance standards to ensure the safe operation of lathe machines. In Russia, the Federal Labour Inspection Service plays a pivotal role in enforcing these regulations, conducting regular audits and inspections to ensure compliance and maintain safety standards.
Key Regulations
- Regular maintenance and inspection schedules to ensure machinery reliability and safety.
- Mandatory use of personal protective equipment (PPE) to protect workers from potential hazards.
- Comprehensive training programs for operators to enhance their skills and awareness of safety protocols.
Role of Technology in Enhancing Safety
Advancements in technology have transformed industrial safety, offering innovative solutions to mitigate lathe accidents. From automated safety systems to real-time monitoring tools, technology plays a crucial role in enhancing the safety of machine operations and protecting workers.
Automated Safety Systems
Automated safety systems can detect potential hazards and automatically shut down machines before accidents occur. These systems utilize advanced sensors and algorithms to monitor machine performance and operator behavior, providing real-time feedback and alerts to enhance safety and prevent incidents.
Future Trends in Lathe Safety
The future of lathe safety lies in the integration of cutting-edge technologies and data-driven approaches. As industries embrace Industry 4.0 principles, the focus will increasingly shift toward predictive maintenance, artificial intelligence, and machine learning to enhance safety and efficiency. These innovations promise to revolutionize the way machines are operated and maintained, significantly reducing the risk of accidents.
Emerging Technologies
- Predictive maintenance systems that anticipate and prevent mechanical failures, ensuring machinery reliability and safety.
- Augmented reality (AR) for enhanced training and real-time guidance, improving operator skills and awareness.
- Internet of Things (IoT) devices for real-time monitoring and data analysis, enabling proactive safety measures and timely interventions.
Conclusion and Call to Action
Russian lathe accidents continue to pose a significant challenge in the manufacturing industry, necessitating a proactive and comprehensive approach to safety. By understanding the causes of these incidents and implementing effective preventive measures, industries can significantly reduce the risk of accidents and protect workers. Prioritizing training, regular maintenance, and the adoption of advanced technologies are key to enhancing safety in machine operations and fostering a safer working environment.
We encourage readers to share this article and engage in meaningful discussions about industrial safety. Your feedback and insights can contribute to the development of better safety practices and help protect workers worldwide. Together, we can create a safer and more efficient manufacturing industry for everyone.
For further information on lathe safety and related topics, explore our other articles and resources. Stay informed, stay safe, and contribute to a safer future for all workers!
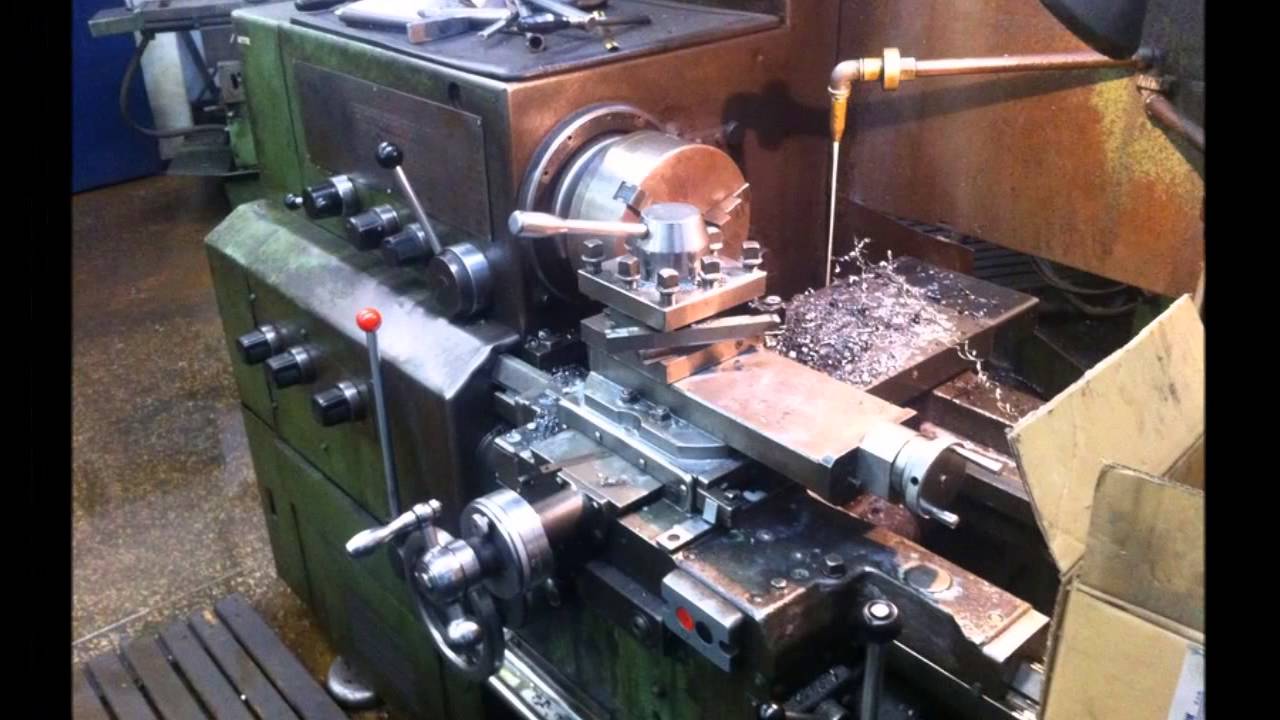
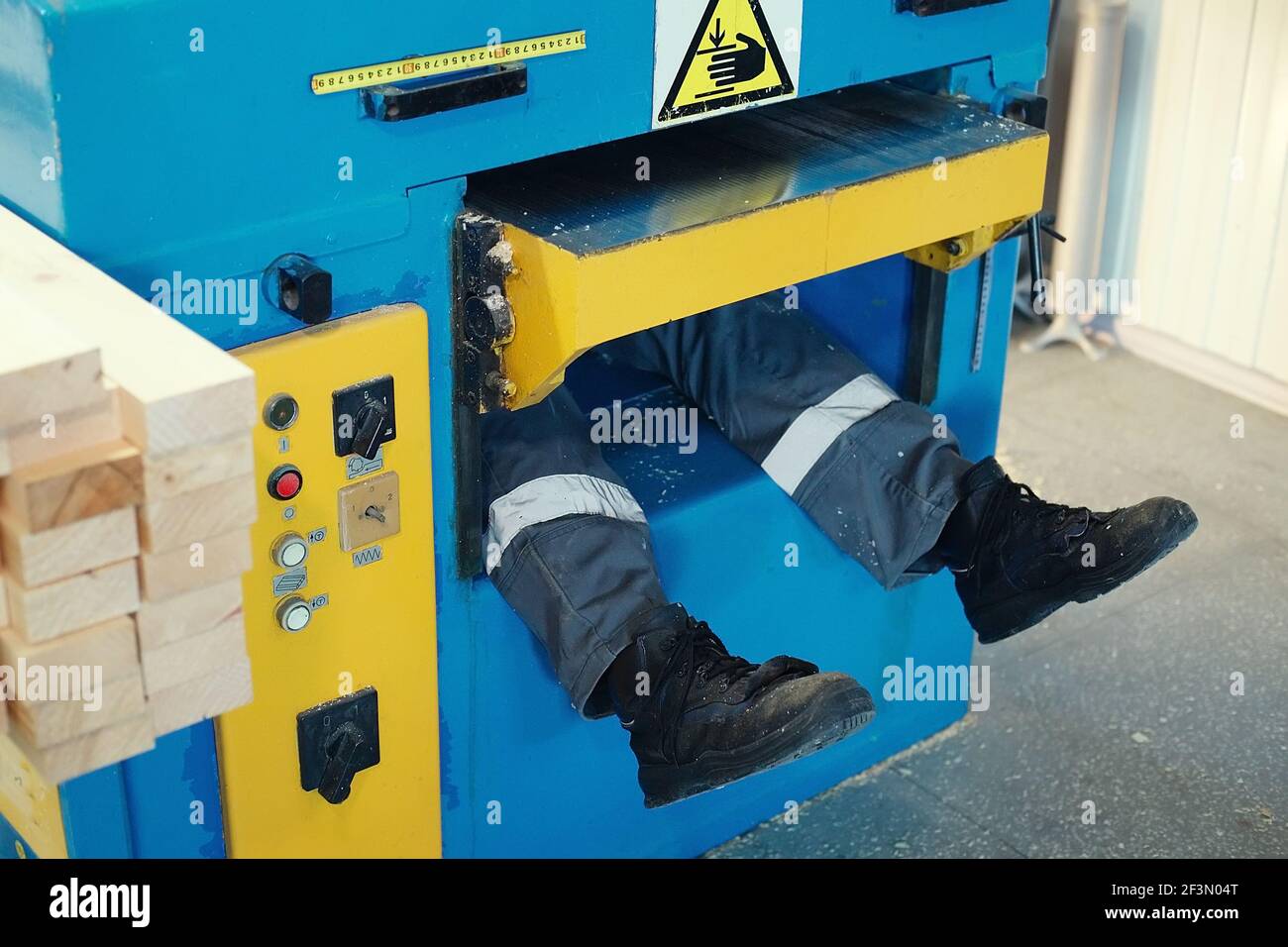
